TEAM
Aware that the success of a company is not given by individuals but by teamwork, Castellari aims to enhance the specific role of each person by making them feel an integral part of the group, as in a big family. Every link in the company supply chain is important. Certainly the product and the consumer are in first place. A heartfelt thanks goes to the agents and their valuable work, to the resellers and dealers with their points of sale and to the suppliers; so that all factors can contribute to our only goal, your satisfaction. Every day they help us make this possible.
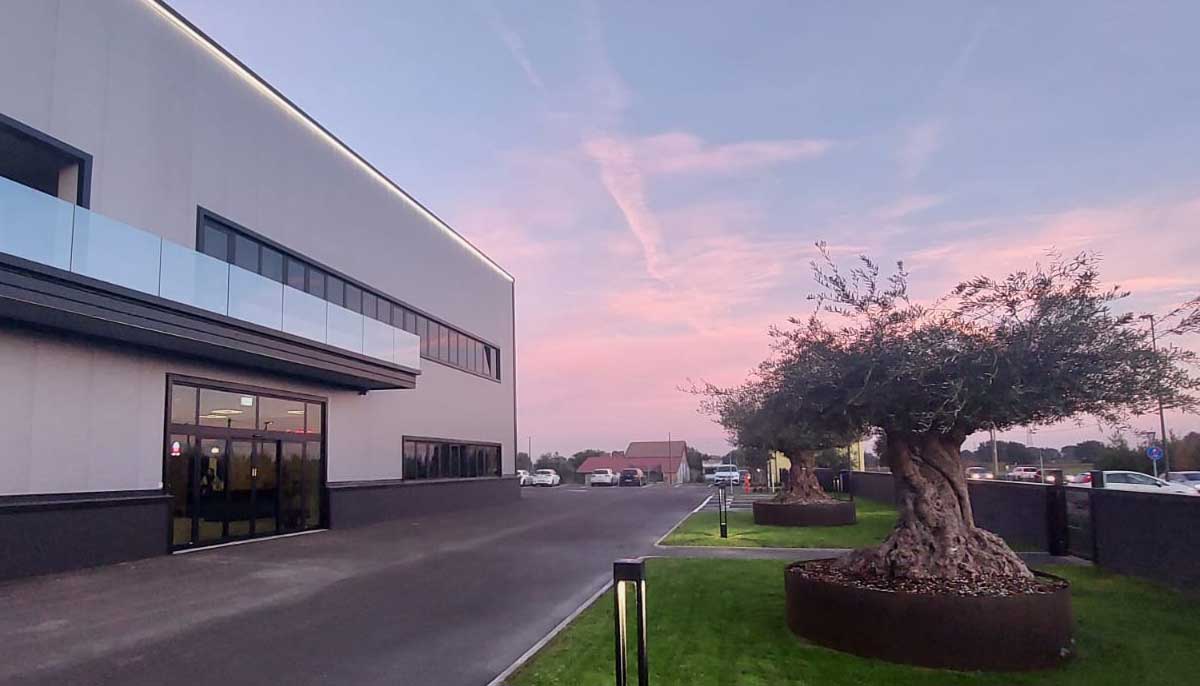
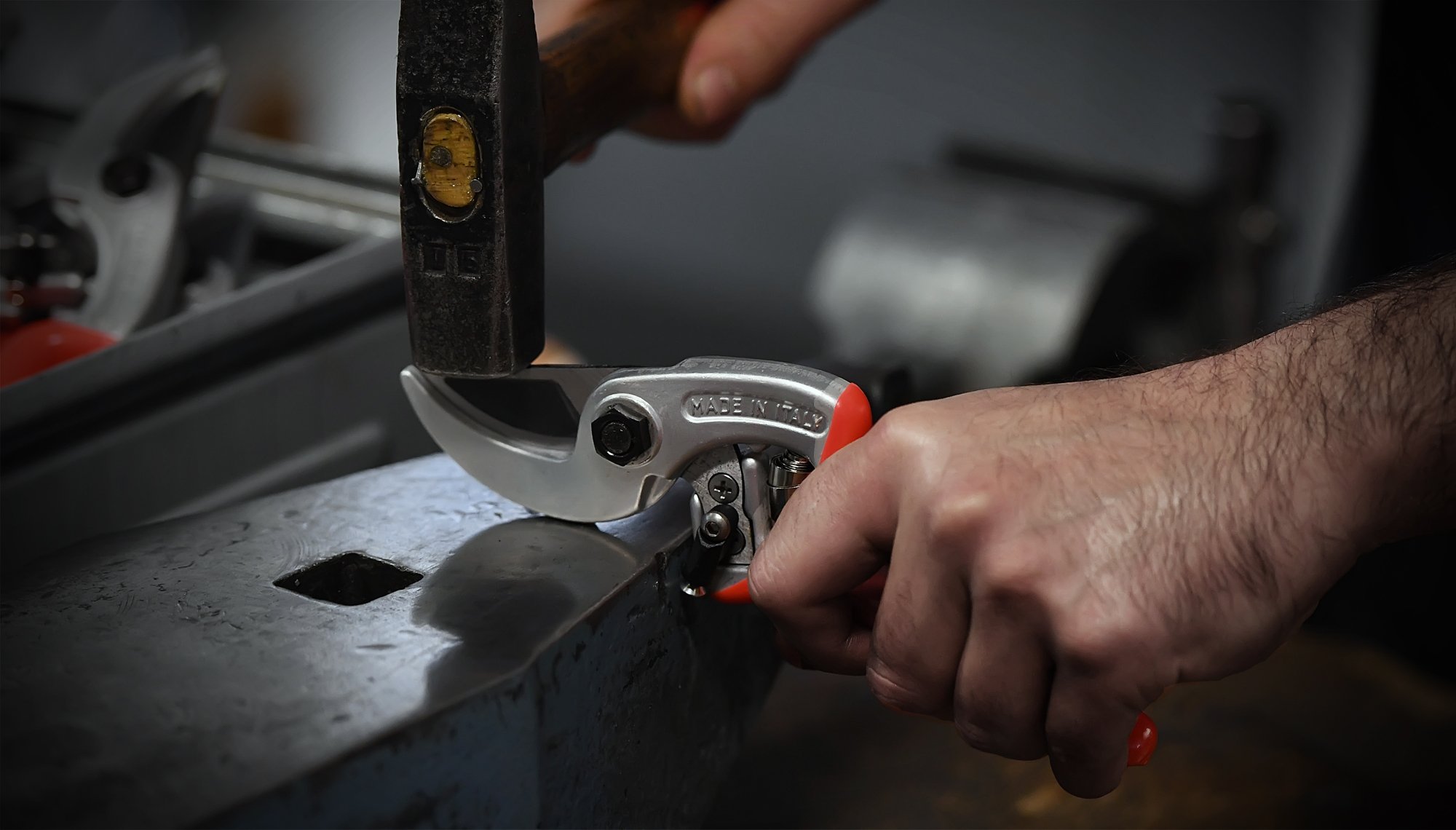
OUR HISTORY
The history of Castellari begins with a small shop in the heart of Imola, “Il coltellino” by Giuseppe Castellari. It was 1976 and many steps were taken to become a structured entrepreneurial reality: 1981 the “LI” scissors products with interchangeable blades are born. 1985 the first branch cutters are created, the TUCANO. 1991 A cavity is excavated in the blades (reduces friction and shear stress). 1996 saw the sum of the technical evolutions in a single product: the UNIVERSAL scissor. 2005 the first model for olive harvesting is produced: Olivance. 2006 apre la seconda sede, con un aumento produttivo di 1800 mq. Oggi, come dall’inizio di questa storia, la Castellari segue le linee della qualità e dell'innovazione interpretando al meglio la Produzione come arte e passione.
DESIGN
New ideas and improvements to the current production take shape thanks to the convergent work between the technical department and field tests. The technical department, supported by the best calculation and design programs, constantly works on the design of new products and the improvement of existing ones, then carrying out specific stress tests on the finished product. Of fundamental importance at this stage, are the opinions and feedback that we receive daily from end consumers. Thus, the result of constant and daily work, the products that will soon become the future of our production are born.
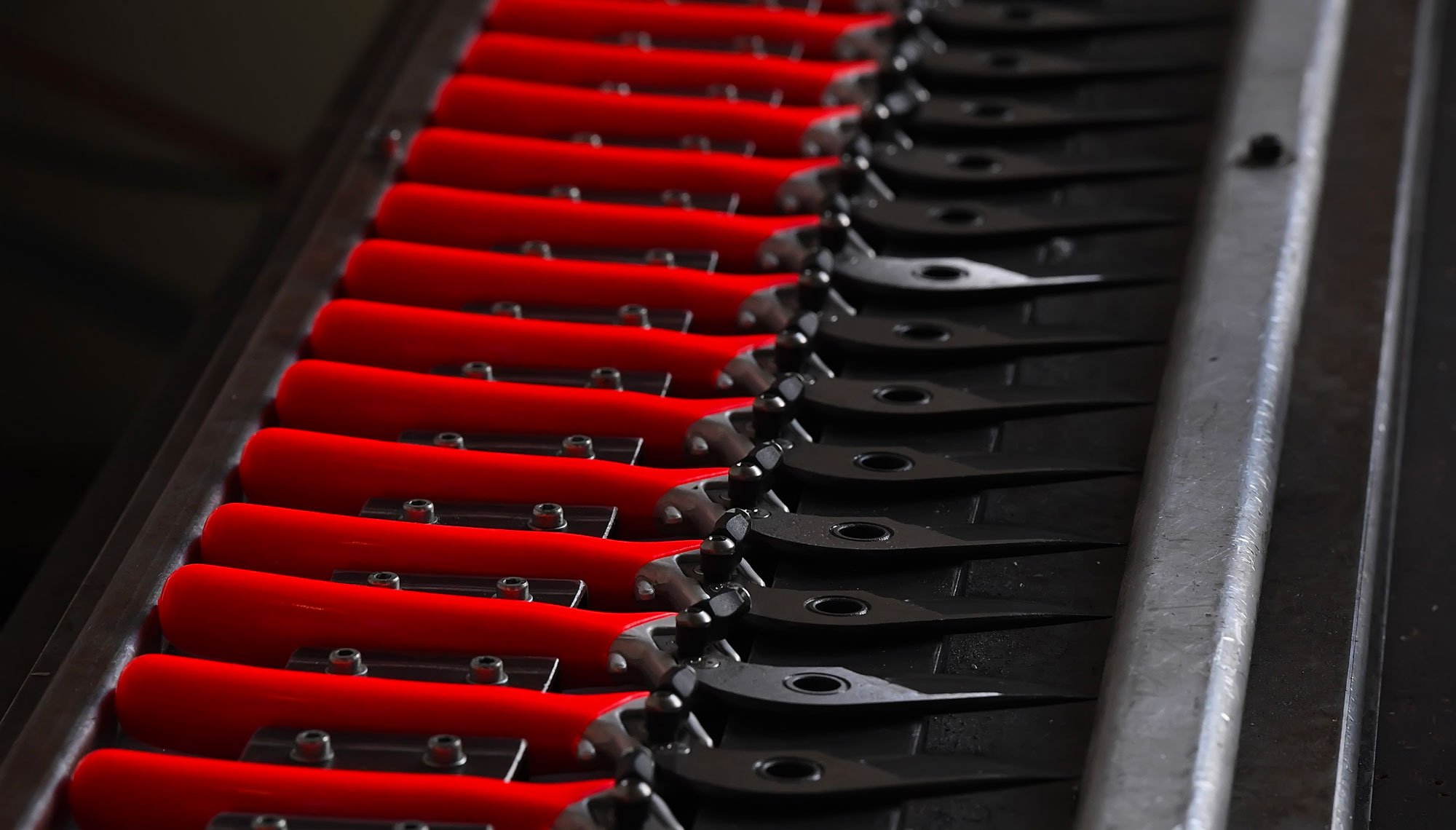
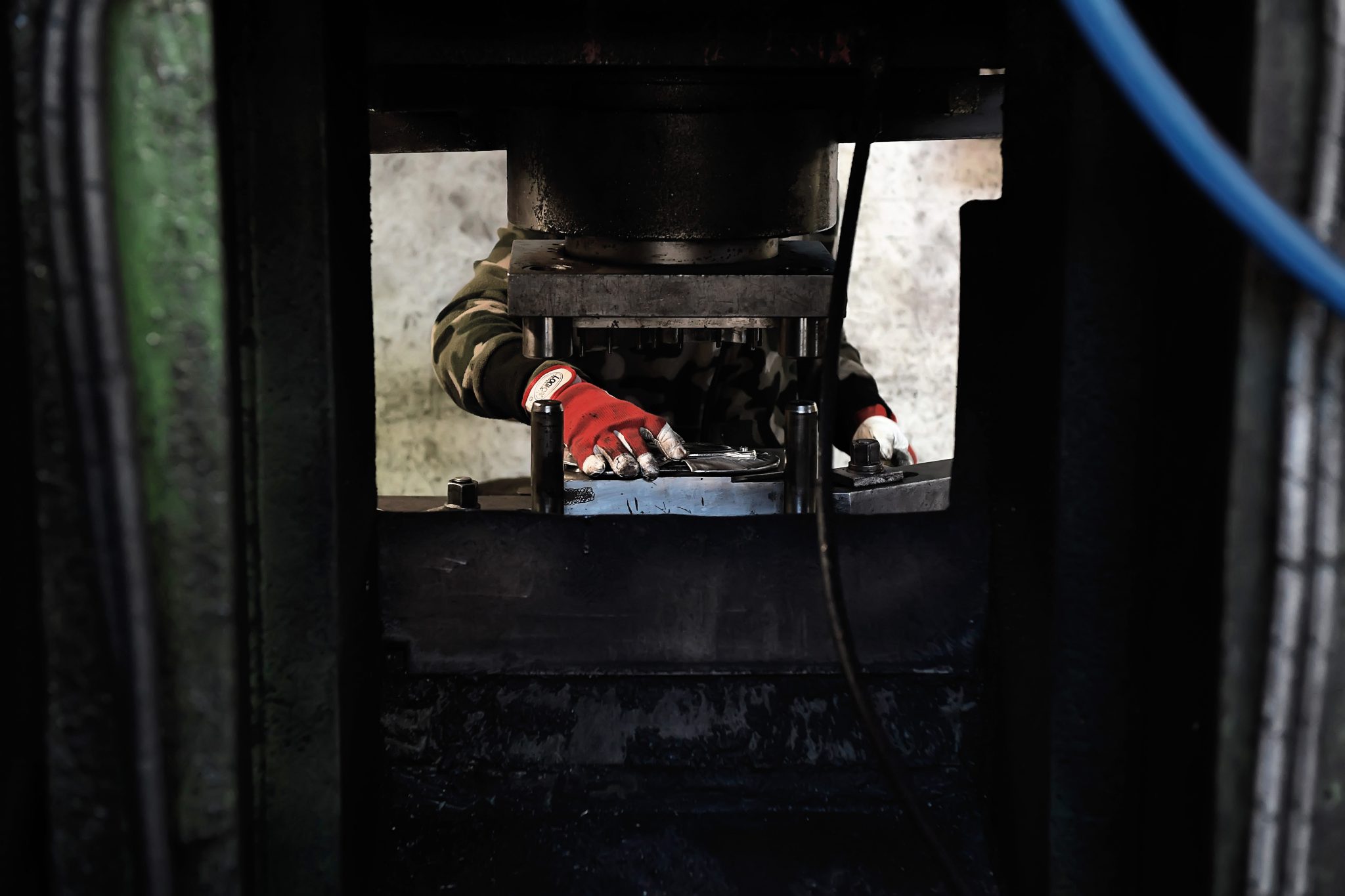
PRODUCTION
We produce scissors, loppers and tools for olive harvesting because it is our passion The quality and resistance of our products derives from the hot forging of steel and aluminum. The heat treatment of the steel gives a perfect mix of 56 HRC hardness and flexibility. The robotic drilling and sharpening processes conclude the internal production chain. These phases are optimized and designed to allow the construction of thousands of pieces per day and ship them to all corners of the globe. Each process tries to respect the value of “made in Italy”, which is an integral part of our business choices since the beginning of our history.
TEAM
Aware that the success of a company is not given by individuals but by teamwork, Castellari aims to enhance the specific role of each person by making them feel an integral part of the group, as in a big family. Each link in the company supply chain is important. Certainly the product and the consumer are in first place. A heartfelt thanks goes to the agents and their valuable work, to the resellers and dealers with their points of sale and to the suppliers; so that all factors can contribute to our only goal, your satisfaction. Every day they help us make this possible.
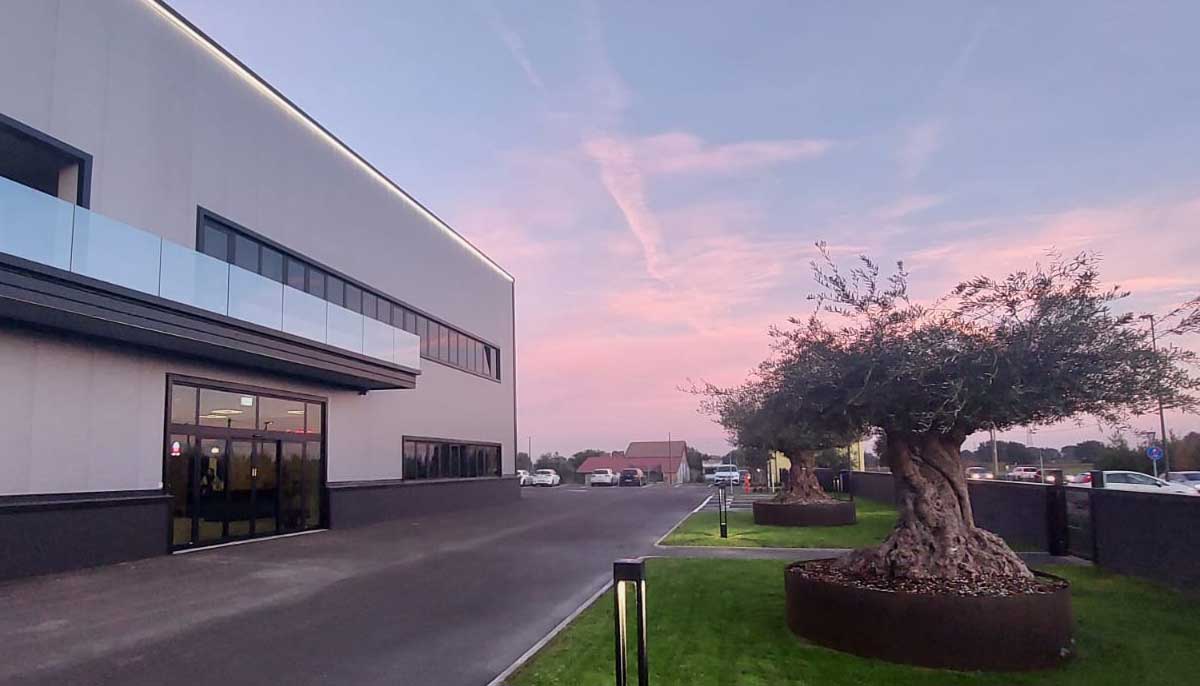
OUR HISTORY
The history of Castellari begins with a small shop in the heart of Imola, “Il coltellino” by Giuseppe Castellari. It was 1976 and many steps were taken to become a structured entrepreneurial reality: 1981 the “LI” products, scissors with interchangeable blades, were born. 1985 the first branch cutters are created, the TUCANO. 1991 A cavity is excavated in the blades (reduces friction and shear stress). 1996 saw the sum of the technical evolutions in a single product: the UNIVERSAL scissor. 2005 the first model for olive harvesting is produced: Olivance. In 2006, the second location opened, with a production increase of 1,800 sq. m. The company over the years still develops making it necessary to further expand and build the new 4000sqm registered office, which took place in 2022. Today, as from the beginning of this story, Castellari follows the lines of quality and innovation, interpreting production as art and passion in the best possible way.
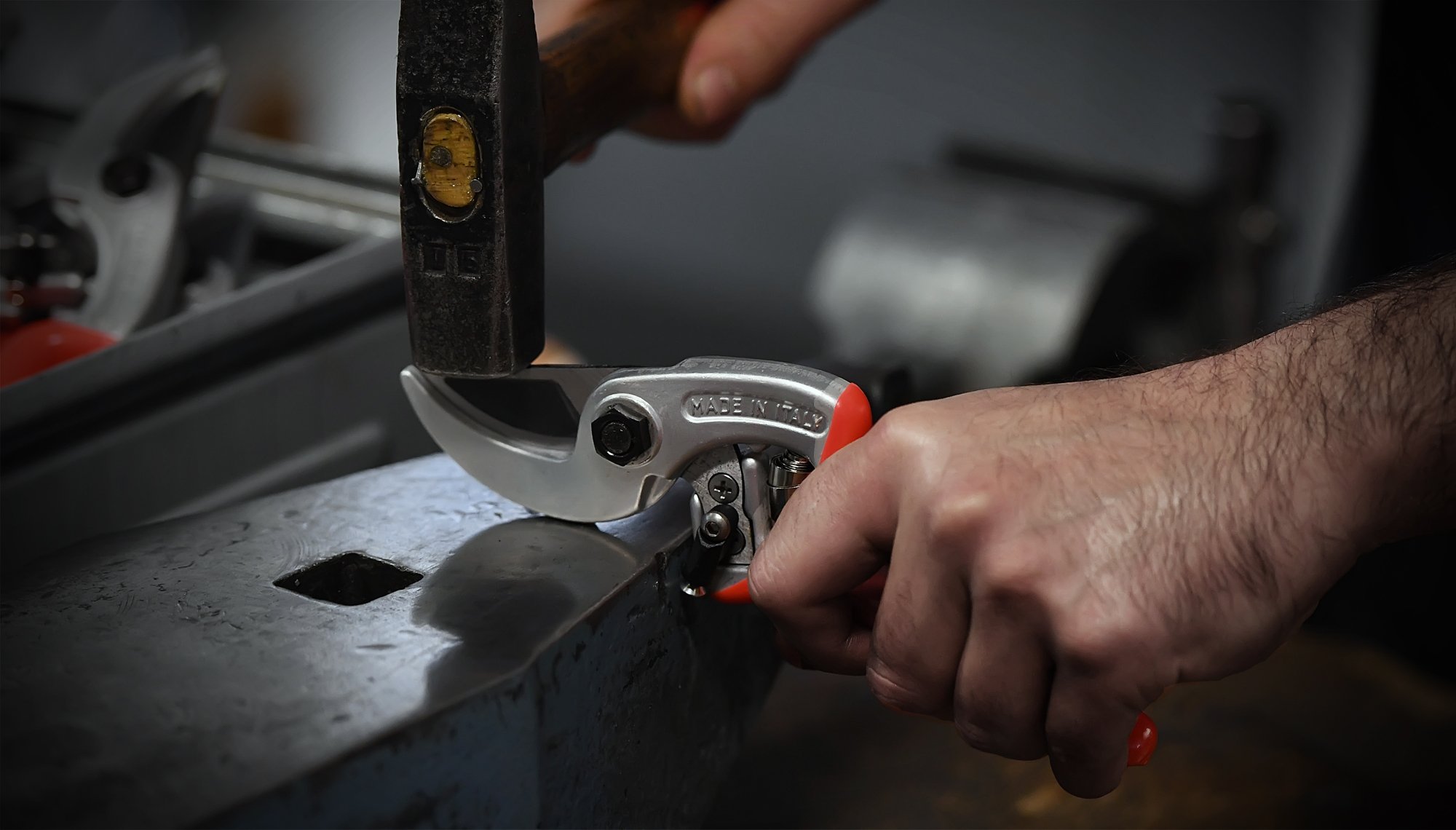
DESIGN
New ideas and improvements to the current production take shape thanks to the convergent work between the technical department and field tests. The technical department, supported by the best calculation and design programs, constantly works on the design of new products and the improvement of existing ones, then carrying out specific stress tests on the finished product. Of fundamental importance at this stage, are the opinions and feedback that we receive daily from end consumers. Thus, the result of constant and daily work, the products that will soon become the future of our production are born.
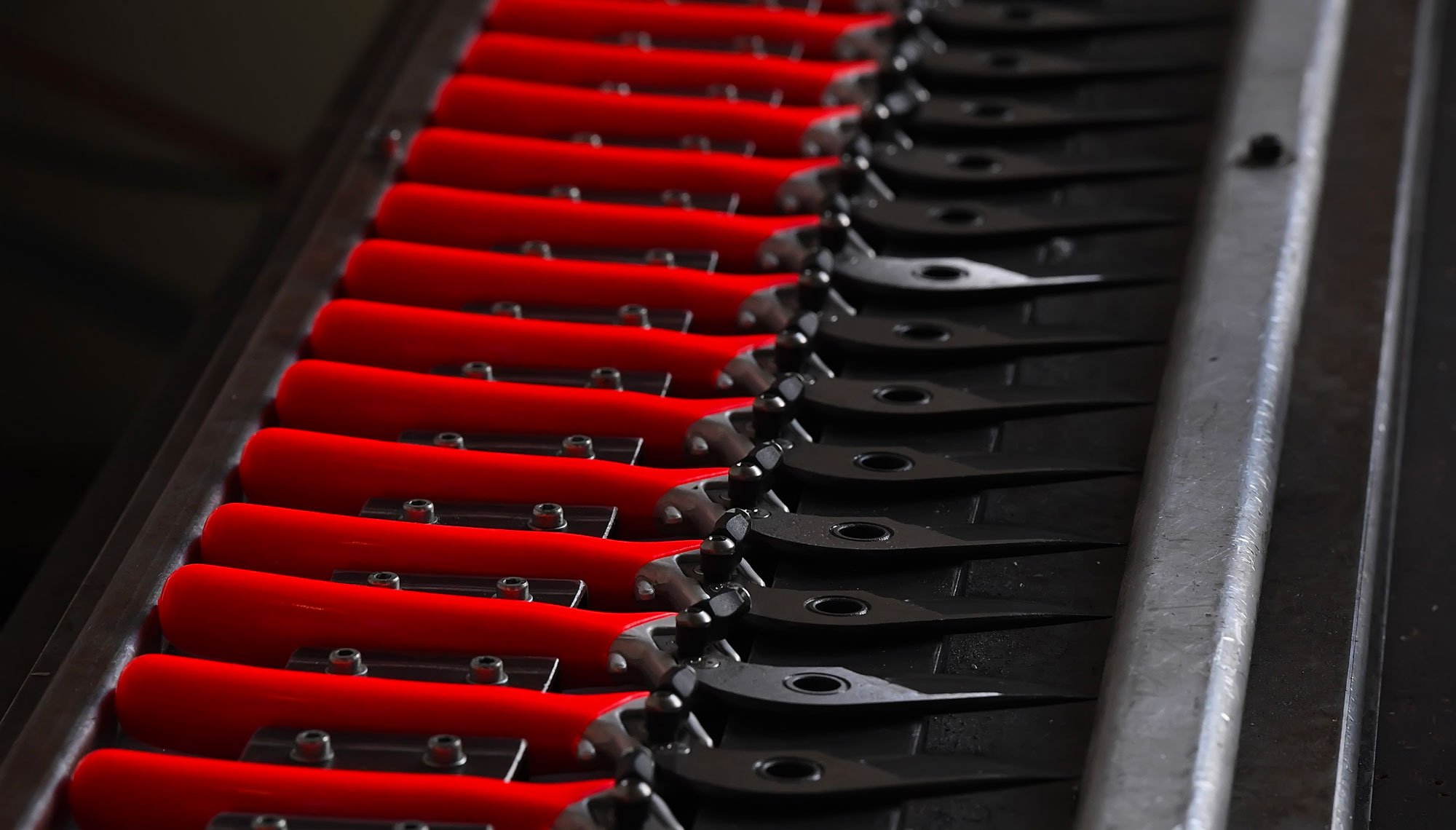
PRODUCTION
We produce scissors, loppers and tools for olive harvesting because it is our passion. The quality and resistance of our products derive from the hot forging of steel and aluminum. The heat treatment of the steel gives a perfect mix of 56 HRC hardness and flexibility. The robotic drilling and sharpening processes conclude the internal production chain. These phases are optimized and designed to allow the construction of thousands of pieces per day and ship them to all corners of the globe. Each process tries to respect the value of “made in Italy”, which is an integral part of our business choices since the beginning of our history.
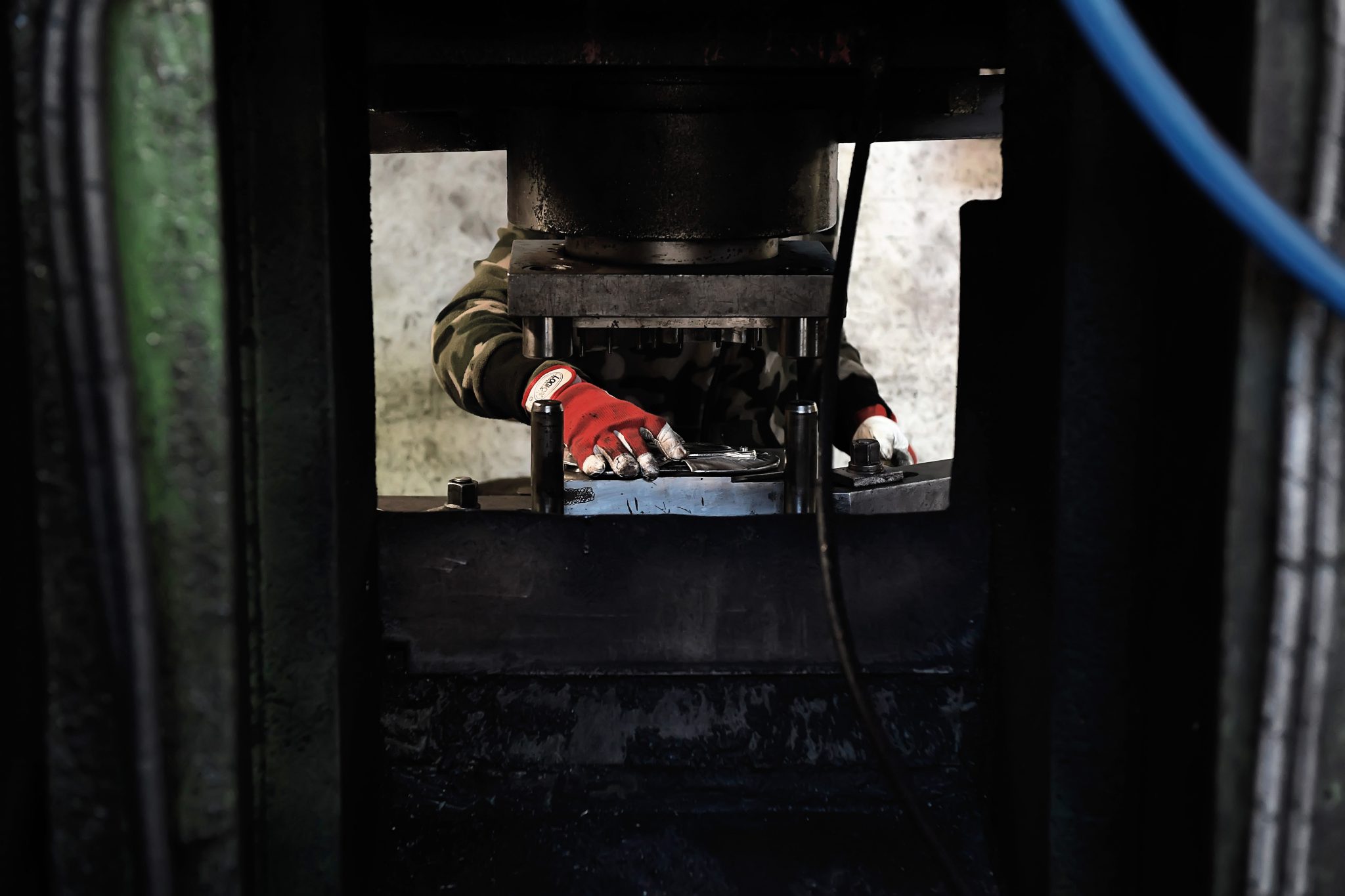